Lapped joint flanges
Nexus Alloys, a distinguished manufacturer and exporter, we understand that seamless and reliable connections are paramount across various industries, ensuring the efficient operation of complex systems. Our expertise lies in crafting a comprehensive range of lapped joint flanges, also referred to as Van Stone or stub-end flanges. These flanges exemplify the fusion of precision engineering and adaptability, making them indispensable in sectors like Aerospace & Defence, Nuclear Power, Oil & Gas, Chemical Industries, Energy & Power, Automotive, Petrochemical Industries, and Fertilizer Industries.
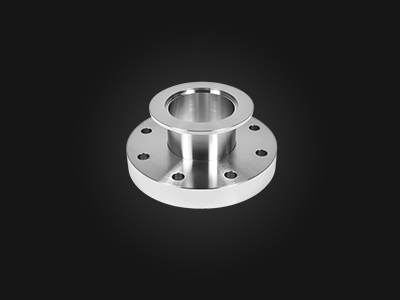
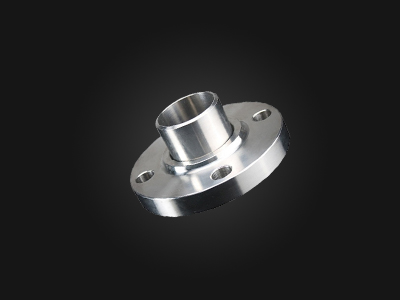
Description:
Lapped joint flanges consist of two integral components – the stub end and the backing flange. Our lapped joint flanges are engineered with meticulous attention to detail, ensuring a seamless fit and robust performance. The stub end is designed with a flared or lap joint, allowing it to effortlessly slide over the connected pipe. Its welding to the pipe ensures a secure and enduring connection. The backing flange, akin to a traditional flange, is equipped with raised faces and strategically placed bolt holes, offering ease of attachment to the opposing component.
Key Features of Lapped joint flanges:
• Versatility: Lapped joint flanges are tailor-made for scenarios demanding frequent assembly and disassembly, streamlining maintenance operations without compromising structural integrity.
• Quick Assembly: The design of lapped joint flanges expedites installation, saving valuable time during critical projects.
• Cost-Effective: The reusability and durability of lapped joint flanges ensure long-term cost efficiency, making them a prudent choice across various industries.
• Reduced Downtime: In industries like Aerospace & Defence, where downtime must be minimized, lapped joint flanges facilitate swift maintenance and replacement.
• Sealing Expertise: While not utilizing a conventional gasket, lapped joint flanges are engineered to provide exceptional sealing, contributing to leak-free performance.
• Customization: At Nexus Alloys, we offer a wide range of materials, sizes, and specifications to match the unique needs of different industries.
Application across Industries:
• Aerospace & Defence: Lapped joint flanges enable quick assembly and disassembly of critical components, ensuring readiness and minimizing downtime in aircraft and defence equipment.
• Nuclear Power: Precision sealing and easy maintenance of piping systems are vital in nuclear power plants. Lapped joint flanges are adept at meeting these stringent requirements.
• Oil & Gas: From pipelines to refinery operations, lapped joint flanges enhance the integrity of connections, supporting the robustness of the oil and gas infrastructure.
• Chemical Industries: In corrosive environments, the durability and ease of maintenance provided by lapped joint flanges ensure the safety and efficiency of chemical processes.
• Energy & Power: Whether in conventional power plants or renewable energy installations, lapped joint flanges offer reliability and swift maintenance.
• Automotive: Automotive manufacturing relies on efficient processes. Lapped joint flanges play a role in ensuring seamless operations in assembly lines and equipment maintenance.
• Petrochemical Industries: Lapped joint flanges contribute to the reliability of petrochemical operations, where safety and performance are non-negotiable.
• Fertilizer Industries: The chemical-intensive nature of fertilizer production demands robust connections that lapped joint flanges provide.
SPECIFICATION:
Nexus Alloys is your trusted ally in sourcing high-quality lapped joint flanges to elevate the performance and durability of your critical operations. Our commitment to excellence and precision engineering makes us the preferred choice across diverse industries. Contact us to explore our comprehensive range of lapped joint flanges tailored to your unique requirements.
CERTIFICATES:
- Test Certificate : Manufacturer test Certificate En 10204 , 3.1 & 3.2
- IBR Test Certificate Form IIIC
STAINLESS STEEL & DUPLEX STEEL LAPPED JOINT FLANGES:
- Size : 1/2″ NB to 48″ NB, ANSI/ASME B 16.5
- Standard : 150# , 300#, 600#, 900#, 1500#, 2500# in ASA 150 & ASA 300
- Stainless Steel : ASTM A 182 F304/304H/304L/316/316H/316L/316Ti/309/310/317L/321/347/904L
- Duplex steel : ASTM A 182 – F 51, F53, F55
ALLOY STEEL, CARBON STEEL & LTCS LAPPED JOINT FLANGES:
- Size : 1/2″ NB to 48″ NB, ANSI/ASME B16.5
- Class : 150# , 300#, 600#, 900#, 1500#, 2500# in ASA 150 & ASA 300
- Alloy steel : ASTM A 182 – F5, F9, F11, F12, F22 & F91
- Carbon steel : ASTM A 105, ASTM A694, F42, F46, F52, F60, F65, F70
- Low Temp.CS : A 350 LF2, A 516 GR. 70
COPPER & NICKEL ALLOYS LAPPED JOINT FLANGES:
- Size : 1/2″NB to 6″ NB, ANSI/ASME B 16.5
- Standard : 150# , 300#, 600#, 900#, 1500#, 2500# in ASA 150 & ASA 300
- Copper Nickel : C70600(90: 10). C71500 (70:30), C71640
- Nickel : UNS N02200, N02201
- Monel : UNS N04400, N05500, Alloy 20
- lnconel : UNS N06600, N06601, N06625, N08800, N08810, N08825
- Hastelloy : UNS N10276, N06022, N10665, N06455
- Titanium Gr. 1,2,3 DTH 3.7025, DTH 3.7035, DTH 3.7055
- SMO 254 Grade UNS S31254
related products
Lapped joint flanges
Nexus Alloys, a distinguished manufacturer and exporter, we understand that seamless and reliable connections are paramount across various industries, ensuring the efficient operation of complex systems. Our expertise lies in crafting a comprehensive range of lapped joint flanges, also referred to as Van Stone or stub-end flanges. These flanges exemplify the fusion of precision engineering and adaptability, making them indispensable in sectors like Aerospace & Defence, Nuclear Power, Oil & Gas, Chemical Industries, Energy & Power, Automotive, Petrochemical Industries, and Fertilizer Industries.
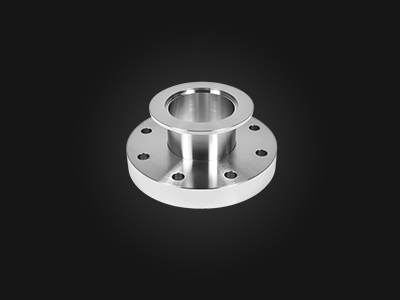
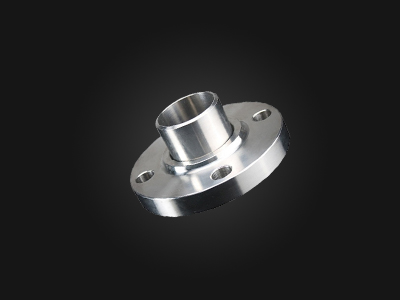
Description:
Lapped joint flanges consist of two integral components – the stub end and the backing flange. Our lapped joint flanges are engineered with meticulous attention to detail, ensuring a seamless fit and robust performance. The stub end is designed with a flared or lap joint, allowing it to effortlessly slide over the connected pipe. Its welding to the pipe ensures a secure and enduring connection. The backing flange, akin to a traditional flange, is equipped with raised faces and strategically placed bolt holes, offering ease of attachment to the opposing component.
Key Features of Lapped joint flanges:
• Versatility: Lapped joint flanges are tailor-made for scenarios demanding frequent assembly and disassembly, streamlining maintenance operations without compromising structural integrity.
• Quick Assembly: The design of lapped joint flanges expedites installation, saving valuable time during critical projects.
• Cost-Effective: The reusability and durability of lapped joint flanges ensure long-term cost efficiency, making them a prudent choice across various industries.
• Reduced Downtime: In industries like Aerospace & Defence, where downtime must be minimized, lapped joint flanges facilitate swift maintenance and replacement.
• Sealing Expertise: While not utilizing a conventional gasket, lapped joint flanges are engineered to provide exceptional sealing, contributing to leak-free performance.
• Customization: At Nexus Alloys, we offer a wide range of materials, sizes, and specifications to match the unique needs of different industries.
Application across Industries:
• Aerospace & Defence: Lapped joint flanges enable quick assembly and disassembly of critical components, ensuring readiness and minimizing downtime in aircraft and defence equipment.
• Nuclear Power: Precision sealing and easy maintenance of piping systems are vital in nuclear power plants. Lapped joint flanges are adept at meeting these stringent requirements.
• Oil & Gas: From pipelines to refinery operations, lapped joint flanges enhance the integrity of connections, supporting the robustness of the oil and gas infrastructure.
• Chemical Industries: In corrosive environments, the durability and ease of maintenance provided by lapped joint flanges ensure the safety and efficiency of chemical processes.
• Energy & Power: Whether in conventional power plants or renewable energy installations, lapped joint flanges offer reliability and swift maintenance.
• Automotive: Automotive manufacturing relies on efficient processes. Lapped joint flanges play a role in ensuring seamless operations in assembly lines and equipment maintenance.
• Petrochemical Industries: Lapped joint flanges contribute to the reliability of petrochemical operations, where safety and performance are non-negotiable.
• Fertilizer Industries: The chemical-intensive nature of fertilizer production demands robust connections that lapped joint flanges provide.
SPECIFICATION:
Nexus Alloys is your trusted ally in sourcing high-quality lapped joint flanges to elevate the performance and durability of your critical operations. Our commitment to excellence and precision engineering makes us the preferred choice across diverse industries. Contact us to explore our comprehensive range of lapped joint flanges tailored to your unique requirements.
CERTIFICATES:
- Test Certificate : Manufacturer test Certificate En 10204 , 3.1 & 3.2
- IBR Test Certificate Form IIIC
STAINLESS STEEL & DUPLEX STEEL LAPPED JOINT FLANGES:
- Size : 1/2″ NB to 48″ NB, ANSI/ASME B 16.5
- Standard : 150# , 300#, 600#, 900#, 1500#, 2500# in ASA 150 & ASA 300
- Stainless Steel : ASTM A 182 F304/304H/304L/316/316H/316L/316Ti/309/310/317L/321/347/904L
- Duplex steel : ASTM A 182 – F 51, F53, F55
COPPER & NICKEL ALLOYS LAPPED JOINT FLANGES:
- Size : 1/2″NB to 6″ NB, ANSI/ASME B 16.5
- Standard : 150# , 300#, 600#, 900#, 1500#, 2500# in ASA 150 & ASA 300
- Copper Nickel : C70600(90: 10). C71500 (70:30), C71640
- Nickel : UNS N02200, N02201
- Monel : UNS N04400, N05500, Alloy 20
- lnconel : UNS N06600, N06601, N06625, N08800, N08810, N08825
- Hastelloy : UNS N10276, N06022, N10665, N06455
- Titanium Gr. 1,2,3 DTH 3.7025, DTH 3.7035, DTH 3.7055
- SMO 254 Grade UNS S31254
ALLOY STEEL, CARBON STEEL & LTCS LAPPED JOINT FLANGES:
- Size : 1/2″ NB to 48″ NB, ANSI/ASME B16.5
- Class : 150# , 300#, 600#, 900#, 1500#, 2500# in ASA 150 & ASA 300
- Alloy steel : ASTM A 182 – F5, F9, F11, F12, F22 & F91
- Carbon steel : ASTM A 105, ASTM A694, F42, F46, F52, F60, F65, F70
- Low Temp.CS : A 350 LF2, A 516 GR. 70